by David Duckworth | Company Culture, Industry
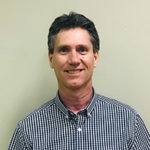
By David Duckworth, Director of Corporate Operations
One of the biggest challenges the food equipment repair industry faces is finding qualified people who can perform the service work. We need technicians that are trained in the basics of electricity, gas, steam, and/or refrigeration who have both mechanical and people skills. Unfortunately, those individuals are very hard to find unless they are coming from another service company and even then we still have to train them our way of doing things. Unfortunately, even after that onboarding, we still have not added someone new to the industry, which results in a net zero gain.
In 2001 we were in dire need of technicians to keep up with our growth. Knowing we would not be able to find people with those qualifications easily. Commercial Kitchen made the decision to try something new: we would train and develop our own technicians internally and pay them to learn. We wanted to teach people the Commercial Kitchen way of performing service from the ground up. We decided to call it Commercial Kitchen University (CKU).
We ran ads searching for people interested in starting a new career. We used a testing program, from a company called Wonderlic, which tested their cognitive skills, personal traits, and mechanical skills to ensure they were the right fit for the program. Once we selected the people who met the qualifications, we followed our normal hiring process of drug screening and background checks. As a member of the Commercial Food Equipment Service Association (CFESA), Commercial Kitchen has access to certification training material for electricity, gas, and steam and we used those materials for our classes.
The CKU program lasts 12 weeks. The first section of the class is critical, teaching the electric portion. After two weeks of studying electricity we tested the students. If the students pass the written exam they were allowed to continue with the program. If they failed they were let go. We wanted them to take the program serious. We were investing a lot of time and money in them. We then moved through the other disciplines of gas and steam. We also included customer service skills and made arrangements with factories to come and train on their specific equipment. We started with 12 people and after 12 weeks we finished with 6. Three of those individuals are still working for us today. Some of them that left us are still in the business and buying parts from us. Everyone agreed the program was a success. We took a break on the program for a while. In 2006 we started talking about restarting the program and developing it into a normal recurring class. We also wanted to centralize all of our training and development into one department. I was promoted to Director of Field Operations and Training/Development in 2006. In 2007 we relaunched the program and graduated 7 technicians.
Over the last 12 years, we have made improvements to the program, including reducing the number of students per class and holding two classes a year rather than one. We have developed work books, power points and hands on training modules, and a variety of equipment to teach with. Since the 2007 relaunch we have graduated over 20 technicians. Charles Moreland was added as the Technical Trainer for the program. He was one of the graduates from the first class in 2001. In 2019 we have one class scheduled starting on August 12th.
It has been great to watch these people develop into great technicians. They now have a skill they can use for a long career in the food service repair business.
by David Duckworth | Company Culture, Industry
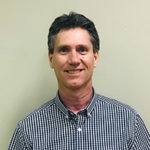
By David Duckworth, Director of Corporate Operations
The Commercial Food Equipment Service Association (CFESA) is a professional trade association comprised of companies who perform service and distribute parts for commercial foodservice equipment manufacturers. The membership is comprised of companies all over the world, but primarily located in the United States, Canada, and Mexico. CFESA places importance on training, sharing of resources, best business practices, and helping create the standard for training used throughout the industry. Their goal is to drive service excellence in the industry.
Of the over 400 members that make up the CFESA organization, a select few have managed to reach the top tier, becoming a Certified CFESA company. Only around 30 or so companies have reached this level of excellence within the association. The process of becoming a Certified CFESA company is stringent. Not only that, but a Certified company will only remain at that level for 3 years before they need to renew that certification. It is sometimes harder to maintain the certification than it is to attain it.
Becoming CFESA Certified is not a simple task. There are a number of criteria which must be met, all of which are graded on a point system during the review process. To begin with, 75% of the business done by the prospective company must be based around parts and service. Second, the company must have been in business and in good financial condition for at least 72 months. The prospective company must also be a voting member of CFESA in good standing before they are eligible to begin the certification process.
The certification has requirements in 5 areas including: financial, education & training, industry participation, industry relations and professionalism. These criteria are measured and calculated using a stringent point system. Here are some of the criteria in more detail:
- Training and Education Standards – This area includes levels of certification on electric, gas, steam, and refrigeration. All technicians employed over 2 or more years must have at least 2 of these CFESA certifications. At least 25% of technicians must be “master technicians”, meaning that they have certifications in three or more of the categories. Technicians must also complete a minimum of two Manufacturer specific trainings within a 3-year period.
- Participation Standards – This area includes regular attendance at CFESA national conferences, speaking at any of the industry conferences, and contributing to the association on one of the various committees. Additionally, contributing to the CFESA magazine and membership on CFESA Board of Directors can also count toward certification.
- Professionalism – A minimum level of insurance is required, and the company must demonstrate it is in sound financial condition. Each office must have a posted mission statement. Stationary, vehicles, emails etc. must have the CFESA logo included to help with brand recognition. All work must carry a 90-day parts and labor warranty.
- This list is far from complete, but goes to show the level of commitment that a company must have in order to attain and maintain the Certified CFESA status. Commercial Kitchen has proudly been a CFESA Certified company since 2004 and just completed the renewal process earlier this year.
Commercial Kitchen Parts & Service is committed to providing fanatical service and unrivaled expertise. Achieving and maintaining the CFESA Certified company status is an example of that commitment.
by David Duckworth | Industry
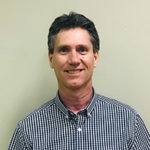
By David Duckworth, Director of Corporate Operations
You have just found that the transformer on a piece of equipment is not producing any voltage on the secondary side, also known as the load side. You check the primary side and you find the correct voltage supply. So you install a new transformer and you’re done, right?
WRONG! You will probably be replacing the new transformer immediately!
A transformer typically does not fail on its own; some other situation or component has caused it to fail. You need to find that problem before changing the transformer.
The majority of transformer failures can be attributed to excessive overloads due to a short circuit on the secondary, or load, side of the transformer. When this load increases, it produces excessive heat beyond the capability of the transformer. This heat buildup breaks down the insulation between the windings, and the transformer eventually burns out, or as we say in the business, “smokes.”
Another reason the transformer may fail is contamination. The transformer can be in a wet or corrosive environment, which may also lead to a breakdown in the insulation of the windings.
Your first step before replacing the transformer is to check the circuitry for any signs of a short circuit to ground and use your ohmmeter to inspect all magnetic coils on contactors, relays, and solenoid valves for any breakdown in resistance. If there is an obvious shorted wire or coil, first correct the problem and then install the new transformer.
If you are not sure what caused the transformer to fail, you will need to temporarily fuse the new transformer. An in-line fuse holder will need to be installed in-line with the hot wire coming off the secondary side of the transformer. Use only fast-blow fuses. You will use a process of elimination to find the problem. Disconnect each component powered by the transformer. Reapply power to the transformer and confirm you have power out of your secondary side. Then start to reconnect each component until the fuse blows. The last part you connect is generally the cause of the transformer failure, and that component will also need to be replaced before replacing the transformer. Remember, it is cheaper to replace a few fuses than a few transformers!
To properly fuse the transformer for the load capability, take the VA rating of the transformer and divide it by the side you are trying to protect.
Examples:
Primary side 60 VA ÷ 120 volts = .50 = ½-amp fuse
Secondary 60 VA ÷ 24 volts = 2.5 = 2½-amp fuse
by David Duckworth | Industry
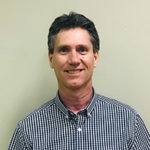
By David Duckworth, Director of Corporate Operations
What Are They Used for?
The majority of all equipment that uses water to generate hot water or steam utilizes some type of water level control. One type is called a low water cutoff control. This control is used to simply shut down the heating circuit if the water drops below a safe level. On electrically heated units, if the water drops below a safe level, the emersion elements would be exposed to the air and burn out (dry fire). When you have a gas-heated unit and the water drops below a safe level, you risk damaging the tank that holds the water.
A water level control has two functions: it allows the tank to automatically fill and maintain water at a set level, and it includes the low water cutoff feature described above. When the unit is turned on, the control senses if there is water in the tank and turns on a fill solenoid if needed. Once the control senses that the safe water level has been reached, it allows the heat circuit to start while it is completing the water fill process.
How Do They Work?
These controls use a transformer, two relays, and two probes to operate. The transformer serves two purposes: it is a step up transformer and an isolation transformer. The primary side (120V), or supply voltage side, has a potential to ground. If you were to read from the hot wire to ground, you would read 120 volts AC. If you were to touch the hot wire to ground, you would experience a dead short. The secondary side (300V), or output side, of the transformer has no potential to ground because it is isolated. In this case, the voltage is created by a magnetic field, so if you were to read either wire to ground, you would read zero volts. If you were to touch either wire to ground, nothing would happen.
One of the wires on the secondary side of the transformer is connected to the body of the tank or grounded to the tank. The other wire from the secondary side is connected to one side of the fill relay coil. The other side of the fill relay coil is connected to a water level probe (short probe) screwed into the tank. The probe is isolated from the tank’s body by plastic or a Teflon sleeve.
When voltage is applied to the water level control, the fill relay’s normally closed contacts supply voltage to the fill solenoid, opening the valve to start filling the tank. When the water reaches the bottom of the water probe, the water AC current flows from the wire connected to the tank’s body through the water to the probe, completing the circuit. The completed circuit supplies voltage to the fill relay coil, energizing the coil and opening the closed contacts and dropping voltage from the fill solenoid. The low water cutoff portion of the control operates the same way, except the heat relay’s contacts are normally open and they close when water reaches the bottom of the long probe. The closed contacts then apply voltage to the heating circuit.
What Will Happen When?
The ground wire to the tank is broken:
If the secondary side wire going from the transformer to the tank body is broken or loose, there would be no continuity through the water to the probes to complete the circuit. The water solenoid would stay energized and overfill the tank with water, and the heat circuit would never energize.
The short probe wire breaks (water level):
If the wire from the short probe to the fill relay coil is broken or loose, there would be no continuity through the water to stop the water fill solenoid. The tank would overfill with water. The heat circuit would still work.
The short probe is grounded (water level):
If the wire or short probe is grounded to the tank body, there would be continuity all of the time in the fill circuit. The tank would never fill with water or the heat circuit would never energize. The water level control acts as if there is water in the tank completing the circuit.
The long probe wire breaks (heat circuit):
If the wire from the long probe to the heat relay coil is broken, there would be no continuity through the water to energize the heat circuit. The tank would fill with water to the proper level. The heat circuit would never activate.
The long probe is grounded (heat circuit):
If the wire or long probe is grounded to the tank body, there would be continuity all of the time in the heat circuit. The tank would start to fill with water and the heat would turn on immediately and could damage the tank or elements.