Planned Maintenance
Our customized Planned Maintenance Programs are designed to protect your investment, minimize equipment downtime, and reduce the overall total cost of ownership.
How Does Our Planned Maintenance Program work?
A lead technician or Fanatical Advocate visits your facility and performs an audit of your equipment. Gathering accurate information (including make, model, serial, voltage, wattage, phase, gas and refrigerant type, etc.) is critical to the success of an effective Planned Maintenance Program. We then develop a customized program that is suited to your unique requirements. A checklist is generated for each piece of equipment outlining specific safety and operational procedures. This checklist is specifically detailed and is performed on each machine in the Planned Maintenance Program during routine visits.
What are the key benefits of our Planned Maintenance Program?
- Designated Account Manager (aka Fanatical Advocate)
- Preferred response times
- Lower maintenance costs
- Energy efficient operation
- Impact on Food Quality
- Impact on Kitchen Staff
- Regular safety check ups
- Fewer emergency calls
- Less down time
- Prolonged equipment life
- Lifecycle cost analysis
- Complete Service History
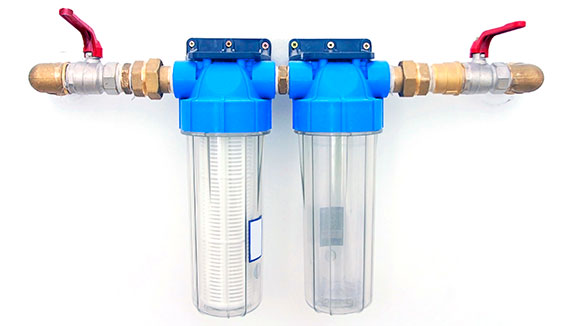
Water Filtration
Filter Systems
Replacement Cartridges